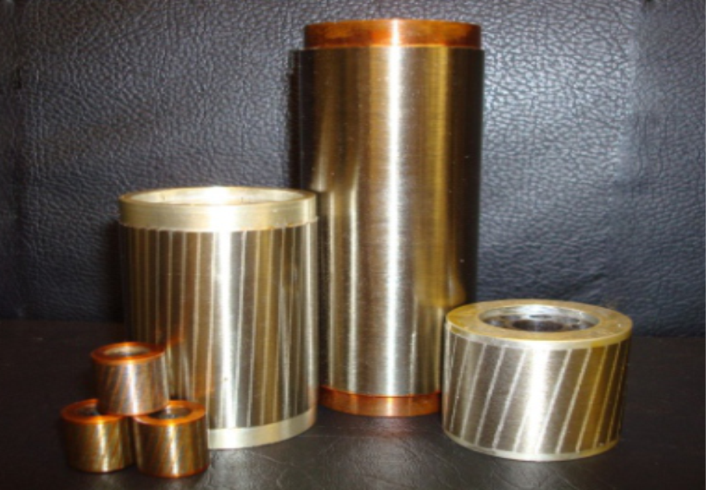
A Game-Changing Rotor Casting Process for High-Performance Applications
Rochester, NY – Arnold Magnetic Technologies, through its Ramco Electric Motors division, proudly highlights RAMCAST™, a proprietary rotor casting process engineered to meet the rigorous demands of aerospace and other high-performance applications. This innovative process establishes an industry standard for rotor manufacturing, delivering ultra-high quality castings with unparalleled precision and performance.
Developed entirely in-house by Arnold’s skilled team, RAMCAST is backed by custom-designed machinery tailored exclusively for this process. Arnold is the only company globally capable of achieving this advanced level of rotor casting. The RAMCAST process produces both aluminum and copper rotors with exceptional quality. It accommodates cast aluminum rotors up to 9 inches in diameter and 35 pounds of alloy pour weight, as well as cast copper rotors up to 9 inches in diameter and 18 pounds of alloy pour weight.
RAMCAST achieves exceptionally low porosity levels of near zero, producing dense castings that ensure structurally sound end rings and enable motors to function at higher speeds and temperatures. The process also achieves tighter dimensional tolerances compared to conventional casting methods, ensuring uniform quality across all rotor designs. These advancements enhance efficiency while minimizing stray load losses, making RAMCAST rotors ideal for demanding aerospace applications.
In addition, RAMCAST resolves issues related to lamination stack inconsistencies often encountered with traditional casting methods. By accommodating individual stack lengths during casting, RAMCAST reduces deformation and minimizes shunting of lamination insulation. This ensures the full utilization of expensive lamination coatings, further enhancing motor performance.
Arnold’s RAMCAST technology enables motor designers to surpass the constraints of conventional rotor casting. By facilitating the production of rotors capable of higher RPMs and temperatures, RAMCAST opens new possibilities for advanced motor designs while maintaining the highest standards of quality and reliability. Each rotor undergoes rigorous monitoring using high-speed data acquisition software, with all data electronically stored for long-term record retention.
About Arnold Magnetic Technologies
Based in Rochester, NY with an operating history of over 130 years, Arnold is a leading global manufacturer of engineered solutions for a wide range of specialty applications and end-markets, including aerospace and defense, general industrial, motorsport, oil and gas, medical, and energy. From its Technology Center and manufacturing facilities located in the United States, the United Kingdom, Switzerland, Thailand, and China, the company produces engineered magnetic assemblies in addition to high-performance permanent magnets, precision foil products, and highly loaded composites that are mission critical in motors, generators, sensors, and other systems and components. Based on its long-term relationships, the company has built a diverse and blue-chip customer base totaling more than 2,000 clients worldwide.
Ramco Electric Motors, a division of Arnold Magnetic Technologies, specializes in manufacturing electric motors and components for industrial and aerospace applications. The company holds ITAR registration and maintains ISO 9001:2015 and AS9100D certifications.
For more information on Arnold, visit https://www.arnoldmagnetics.com.
For more information on RAMCAST, visit: https://www.arnoldmagnetics.com/electric-motors/ and https://www.arnoldmagnetics.com/wp-content/uploads/2025/01/Ramcast-Datasheet-4-06-23.pdf.