Halbach array solutions
March 07, 2022
There is a longstanding, general trend of replacing internal combustion engines, hydraulic or pneumatic motors and drives with advanced electric motor systems. The driving force behind this is the need for more energy-efficient systems, which typically lower operating costs, reduce overall emissions and enhance performance.
The main selection criteria are energy efficiency, power density and cost of electrical motor technology. There are three main electrical motor topologies to consider, with vast potential for surface permanent magnet (PM) motors to provide performance and energy efficiency required to unleash the latest electrification application.
Motor topology selection
Of the various modern electrical motor technologies, the most common three are induction machine, surface PM and switched reluctance. As indicated by Figure 1, both induction machine and switched reluctance topologies allow for relatively simple construction, low cost and no need for PM excitation when compared to surface PM topologies. However, neither induction machine nor switch reluctance topologies can deliver the same level of energy efficiency, torque control and torque-inertia ratio as surface PM topologies.
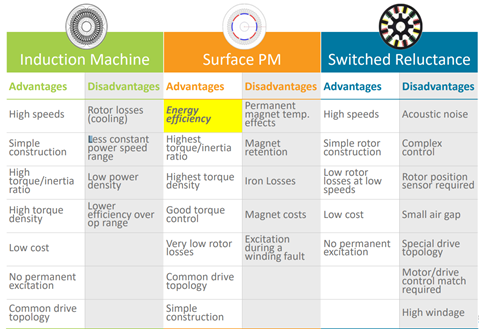
With surface PM topologies, however, PMs are necessary and present several considerations and challenges that must be overcome. A pertinent consideration with surface PM motors is that PMs generally reduce magnet field strength as temperature increases.
Features of surface PM electrical motor topologies
Fortunately, there are adequate design-freedom and surface PM variations that can boost surface PM motor efficiency, manufacturability and other features altogether. For instance, when comparing Halbach and parallel magnet surface PM motors, parallel magnet torque is dictated by magnet width, where torque ripple is also sensitive to magnet width (Figure 2). This relationship limits parallel surface PM motor design when designing for optimal flux.
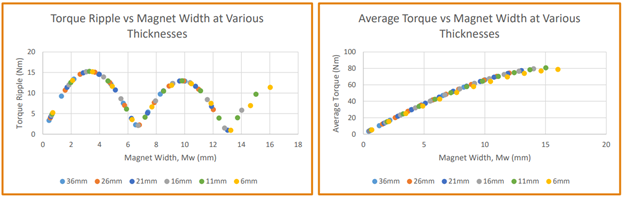
However, a multi-segment Halbach magnet array can provide high flux in a compact space, especially if wedge-shaped magnets are used. Although linear Halbach array behavior is well defined, precision magnetic finite element analysis (FEA) is needed to optimize the performance of round rotor Halbach arrays. It can be seen in Figures 3 and 4 that the overall magnetization pattern results for the radial flux density at 1 mm distance from the rotor surface indicate that the lowest flux density option is the parallel magnet pattern, and that the all wedge-shaped pole and tangential magnet four-segment Halbach array perform close to the ideal Halbach array pattern. This demonstrates that a four-segment radial Halbach array rotor can provide greater performance while minimizing manufacturability difficulty and even cost.
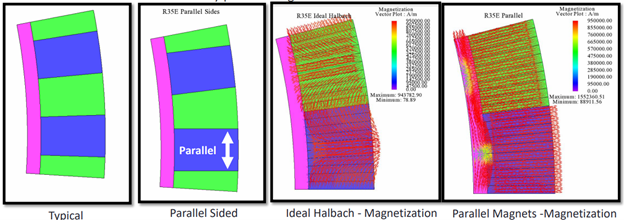
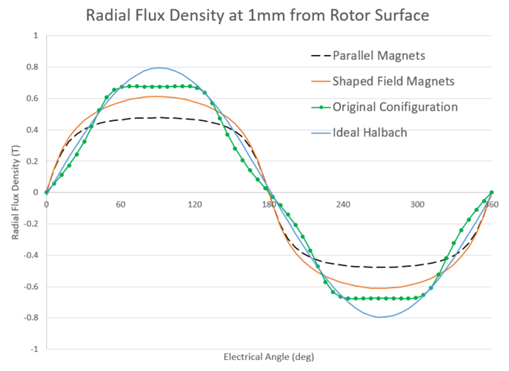
Figure 5 shows an example four-segment Halbach array with wedge shaped pole and tangential magnets. The following data comparing various configurations of a four-segment Halbach array is used as an example of how surface PM motor topologies can be configured to optimize manufacturability, cost and power density. In this comparison, the graph results are normalized based on the ratio of the pole magnet (Spm) at the outer radius of the rotor and the arc length divided by the pole pitch (Spp). For reference, an Spm/Spp ratio of 0.0 would indicate only tangential magnets are used and a ratio of 1.0 would be that only pole magnets are used.
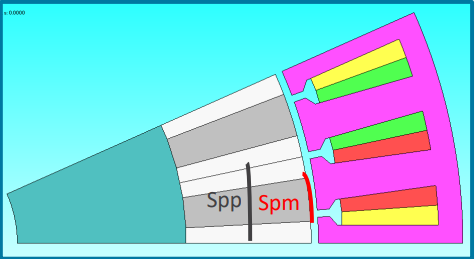
The results of the study show that using a combination of wedge/rectangular tangential and pole magnets and even a combination of Recoma (R) 35E and lower strength Recoma (R) R30 can enable high performance surface PM motors that benefit from lower cost and greater ease-of-manufacturing while also enhancing torque compared to the all-wedge and all Recoma (R) 35E configuration (Figure 6).
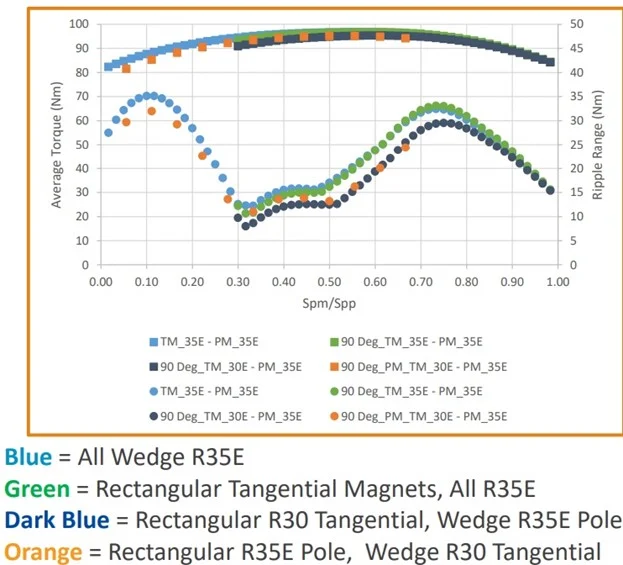
Conclusion
Radial and multi-segment Halbach array surface PM electrical motors exhibit excellent performance characteristics while providing energy efficiency for emerging automotive, aerospace and other applications. With thoughtful design, material selection and the latest magnetic technologies, these motors can be made to fit an extremely wide range of use cases and can even be optimized for cost and manufacturability as well as performance.
Originally Published on Engineering360